Concrete Degradation
A summary of decomposition and failures of OPC (Ordinary Portland Cement) Concrete.
It is our goal at Navrattan to overcome these weaknesses.
Portland Concrete Degradation may have Various Causes
•Fire and High Heat
•Radiation
•Aggregate Expansion
•Sea Water Effects
•Bacterial Corrosion
•Calcium Leaching
•Chemical Damage
Carbonization
Chlorides
Sulfates
Distilled water
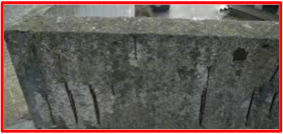
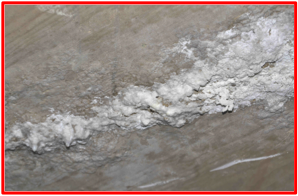
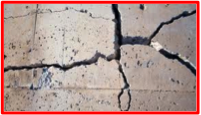
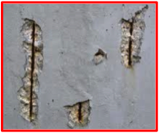
Thermal Damage
• 0º to 300º c - OPC undergoes normal Thermal Expansion. Above that temperature shrinkage occurs due to water loss.
• 300º to 500º - major changes are carbonization and coarsening of pores
• 450º to 550º - cement hydrate decomposes, yielding Calcium Oxide
• 573º - Quartz undergoes rapid expansion
• 600º - Calcium Carbonate Decomposes, causing rehydration of the CaO
• At 900º Calcite starts shrinking due to decomposition
• Concrete with high moisture content will explode with fire causing spalling cracks.
• Concrete that turns pink from fire should be replaced
Radiation
Exposure of concrete structures to neutrons and gamma radiations in Nuclear Power Plants can induce radiation damage.
Paramagnetic defects are easily formed, but very high fluxes are necessary before significant mechanical damage is observed.
Aggregate Expansion
• Minerals can react with Alkalis coming from the hardened concrete, especially:
Basalt, Silica, Opal, Chalcedony, Flint, and Quartz
• Following the Alkali/Silica reaction
(ASR) a gel forms that can cause
extensive cracks. ASR’s can cause
pop-outs at about 1” diameter.
•Dolomite (Magnesium Carbonate) aggregates react with hydroxyl ions, forming magnesium hydroxide and a carbonate ion, causing an expansion.
• Pyrite (iron sulfide), with acidic permeations thru the concrete, expand, re-crystalize, and form iron oxide and ettringite, causing cracks.
Corrosive ReBars
• Expansion of Corrosive products namely Steel ReBars, may induce Mechanical Stress, which in turn causes cracks.
• ReBars installed too close to surface corrode more quickly due to higher moisture and an acidic environment, causing spalling cracks and separation from the steel.
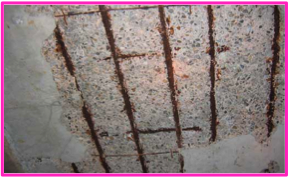
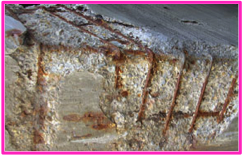
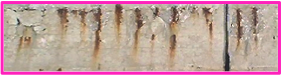
Chemical Damage from Carbonization
• Carbon Dioxide from the air can react with the calcium hydroxide to form calcium carbonate (limestone), which is the reversal of the clinkering process used in making OPC.
• Carbonization is a slow and continuous process which limits the life expectancy of OPC Concrete to approximately 80 years.
• Carbonization increases mechanical strength, but at the same time can decrease alkalinity to a PH of below 10, which allows the corrosion of the steel.
Chlorides
Calcium Chloride used as an accelerator, especially during cold weather, and Sodium Chloride to a lesser extent have been know to leach Calcium Hydroxide and weaken the chemistry of the OPC.
Another big problem with Chlorides,
being mildly acid, is their attack on
Steel Re-Bars or Steel Mesh.
Sodium Chloride used for snow melting is very corrosive to Concrete.
Salts are hygroscopic and attract and retain water by opening the pores thus becoming an inroad to freeze/ thaw damage , especially surface flaking.
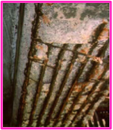
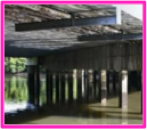
Sulphates and Sulphur
Sulfate solutions (Acidic) can cause damage
To OPC by weakening the binder in its gel stage,
and also is corrosive to hardened concrete.
One of the worst destroyers of concrete is when bacteria reduce hydrogen sulfide gas to a film, which penetrates the pores and cracks, especially in sewer mains.
Acid rain is also high in sulfuric acid after sulfur dioxide in the air combines with the rain.
OPC contains a small percentage of gypsum (calcium sulfate dehydrate). The sulfate in the OPC is an internal source, and is activated when the internal temperature of the curing concrete reaches 160 degrees Fahrenheit, a condition which can and should be avoided.
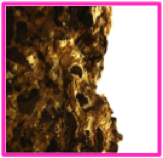
DeCalcification due to Distilled Water
Distilled water can leach calcium from OPC, leaving the concrete brittle. Common sources of distilled water are steam itself and condensed steam (distilled) water.
Distilled water does not contain any calcium ions so it attracts and leaches them out of the cured concrete.
NHPC and NWC
Is Hydrophobic – water penetration is very low
Is Anti Microbial – Bacteria does not grow on it
Is Fire proof – Can withstand high temperatures
Prevents corrosion – Steel will not rust
Has a built in polymer sealer
Like Roman cement, which is over 2000 years old, has No Rebar and No Cracks
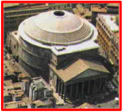
The Panthenon